A water jet is a kind of high-pressure cutting process used to cut various materials, including plastic, wood, metals, and a variety of other materials. It uses an incredibly high-pressure jet of water or a mixture of water and an abrasive substance. The water jet is more versatile and is ideal for cutting materials such as plastic, metal, wood, and even stone. Its advantages and limitations are explained below.
High-pressure water jet
High-pressure micro max water jet cutting is a versatile tool that is used in numerous industrial applications. It uses high-pressure tubing that offers excellent yield and tensile strength as well as a smooth interior surface. Typically, high-pressure tubing is made of cold-worked stainless steel or thermoplastic pressure hose. The length of high-pressure tubing can vary from 0.25 inches to 0.563 inches.
The technology is widely used in industries such as stone and tile cutting, jet engines, and even oil pipeline cleaning. Its development dates back to the late 1960s and early 1970s, when basic equipment for high-pressure waterjets was developed, including high-pressure pumps and high-pressure pipe fittings. Waterjets became increasingly popular in the 1970s, as more automotive manufacturers sought to increase their output value and support their production cycles.
Water jet cutting has several advantages over other cutting methods, including accuracy, safety, and cost. It is also capable of cutting extremely complex shapes and thermally sensitive materials. High-pressure water jet cutting eliminates the need for downtime and allows for fast turnaround. Further, water jet cutting is safe for use in the food processing industry. It does not involve the use of chemicals, cutting tools, or other materials that could potentially come into contact with food.
High-pressure water jet cutting is often called “waterjet” because of the water-powered stream that is used in it. The water-powered stream has a number of advantages over other cutting techniques, including flexibility in part design and abrasives that can reduce material loss. It is also a safer alternative to plasma cutting. The benefits of used waterjet cutting machines are plentiful. And its advantages outweigh the drawbacks.
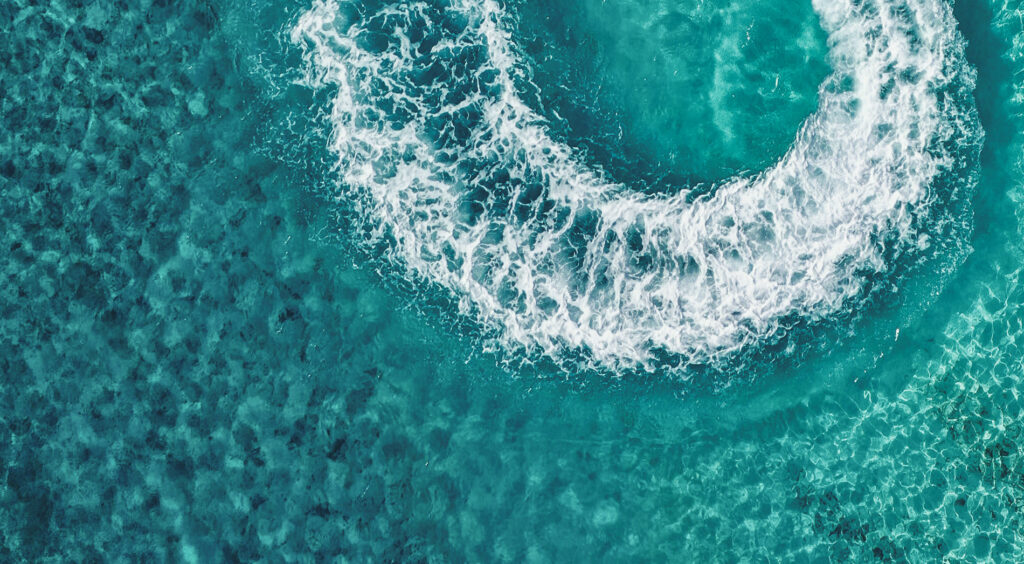
Environmentally friendly
Waterjet cutting technology has several environmental advantages. Compared to other cutting methods, water jet cutting requires less water. Depending on the size of the orifice, water consumption can range from half a gallon per minute to several gallons per minute. Water jet cutting systems can also be configured to recycle cutting water. These features contribute to reducing the environmental impact of waterjet cutting. In addition to this, the process is safe to watch.
Waterjet cutting also helps reduce waste, as it uses abrasives to increase the cutting power of water. These abrasives, such as garnet, are non-hazardous and can be safely disposed of in landfills. However, in some cases, if the workpieces being cut are toxic or hazardous, special requirements must be met. To minimize the environmental impact of waterjet cutting, companies should ensure that waterjet cutting processes follow local and state regulations.
When cutting metal, waterjet cutting can save both money and resources. Since waterjet uses a natural garnet abrasive, it reduces water usage dramatically. The water used in cutting is purified before reused. To find out more about waterjet cutting, please contact a supplier of your choice. They will be happy to give you a quote and delivery time. These are just a few of the many benefits of waterjet cutting.
Waterjet cutting produces a smooth edge with no burn marks, excess burrs, or cracks. Since waterjet cutting is a cold process, it does not produce toxic emissions or other harmful toxins. Additionally, waterjet cutting protects the operator from injury. This precision cutting method is effective for a wide range of industries. It is also an ideal choice for jobs that require precision cutting and intricate designs. If you’re looking for an environmentally friendly way to cut metal, waterjet cutting is your choice.
Cost effective
There are several benefits to using waterjet cutting for your manufacturing projects. It produces a clean cut with minimal chipout. Because the waterjet cutting process does not alter the material’s structure, it is extremely precise. It is also an excellent choice for cutting delicate electronics. This process can cut plastic and metal to make electronic components, such as circuit boards and insulation. The cost savings of waterjet cutting is enormous. And as the technology continues to advance, more manufacturers are switching to this method.
Waterjet cutting has many benefits, including its ability to cut almost any material, while minimizing material waste. Unlike traditional methods, waterjet cutting does not require secondary finishing. The process also produces a superior edge. Waterjet cutting also does not lead to material degradation, such as crushing, chipping, or burning. It also requires no special knowledge or training. Moreover, you can cut more complex and intricate parts using waterjet cutting than ever before.
The downsides of waterjet cutting are that it is less precise than laser and plasma cutting, which means you will have higher chances of part defects. And, unlike laser and plasma cutting, waterjet cuts do not result in thermal stress or burning. As a result, the surface finish is smooth and without a heat-affected zone. In addition, the waterjet cutting process is more expensive than laser cutting. However, its speed is higher than laser cutting.
Another major drawback of water jet cutting is that it creates a huge mess that requires a lot of cleanup afterward. Moreover, because water jet cutting processes combine abrasive materials, water jet cutting is often not recommended for small-scale businesses. Moreover, water jet cutting requires more space than laser cutting, which can be a barrier to funding. So, if you are thinking of buying a water jet cutting machine, it is best to think about what you can cut before making a decision.
Limitations
Generally, waterjet cutting limits are 0.001 inch (0.025 mm) or less. However, these limits are rarely realistic. When cutting straight lines, it is possible to ignore the limits and keep the part straight. But near corners, waterjet cutting limits become important. The waterjet must slow down as it approaches the corner to become perpendicular to the material. Boosting its speed out of the corner can mar the part and cause it to bend.
Despite the relatively low abrasive pressure required by a waterjet, there are some materials that are incompatible. For example, tempered glass is unsuitable for waterjet cutting. Other types of glass can be cut with a waterjet. However, tempered glass is incompatible with the abrasive jet. So, in cases where tempered glass is needed, a more traditional waterjet cutting solution is preferred.
The waterjet’s precision is built in with its precision table. Controlling the jet is another key to precision. Waterjet cutting speeds are greatly increased by sophisticated software. A high-quality waterjet machine can compensate for the “floppy” air and water used in the cutting process. But the waterjet still has its limitations. For example, waterjet cutting limits should be within 0.002 inches. This is far too close to the desired tolerance for many materials.
There are several parameters to consider when waterjet cutting metal. One important parameter is the maximum Z-axis travel. Waterjet cutting machines can be made to cut up to 2 inches of material, but a larger abrasive jet can produce parts that are more accurate and more expensive. The speed of cutting also affects the price of a job; higher speeds and greater accuracy take longer to produce. And while the speed increases, the quality of cut edges decreases.
Safety
Although waterjet cutting is not prone to the same hazards as welding and forming, users should follow basic safety practices. For example, they should wear ear protection while not submerged in the water stream. They should also carry a medical alert card with them when working near pressurized equipment. They should also avoid walking on the material support slats or loading equipment. Lastly, they should keep the cover closed and follow the normal lockout/tagout procedures.
One of the most common accidents that occur during waterjet cutting is the use of improper safety precautions. The water jet’s stream is so powerful that it can sever body parts. A waterjet operator must carefully check the area for body parts before starting the cutting process. While water jets are designed to produce relatively low noise levels, they can still cause injury to the eyes, especially if the cutting happens at high speed. Using protective goggles is important in these situations.
The water jet cutting stream can penetrate many strong and hard materials. The water jet cutting stream can cause injury to the user, so they should wear ear protection when working near them. If the cutting process goes wrong, the nozzle can crush body parts. When working near a waterjet cutting head, it is best to work on a board or catwalk. Aside from safety gear, people should wear a protective face mask.
When using waterjet cutting equipment, it is important to follow the manual carefully. Some waterjet cutting machines can cover 100 inches per minute. While this may seem like a lot, it is still fast and can injure someone. Keeping your hands away from the machine and the nozzle should be properly grounded is essential. Never use an electrical plug adapter with waterjet equipment. If you must operate waterjet equipment, make sure to disconnect the main power supply before operating it.